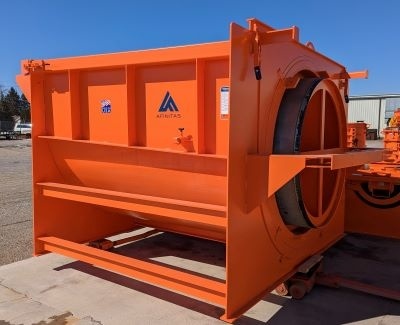
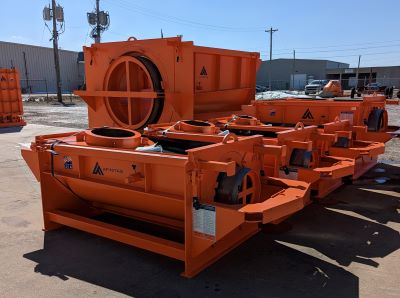

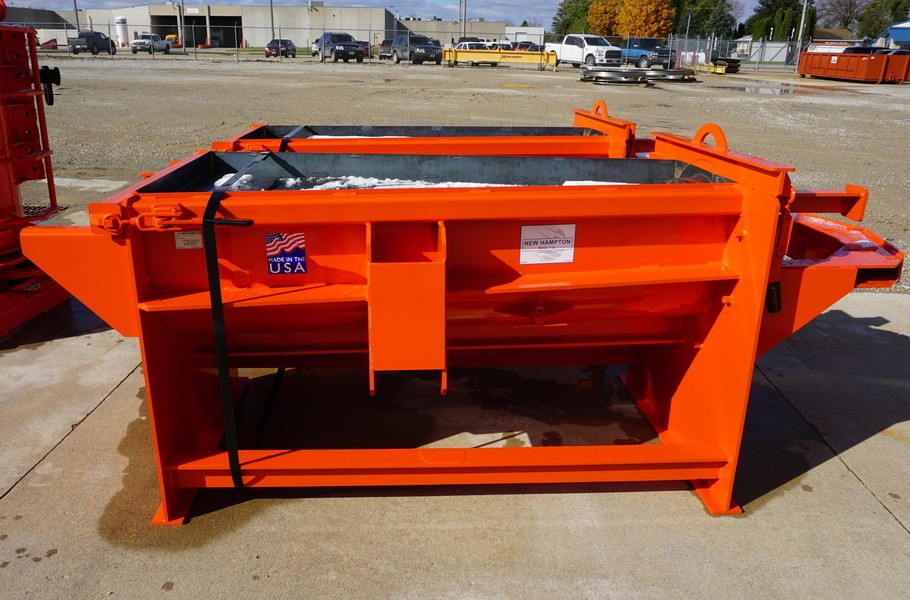
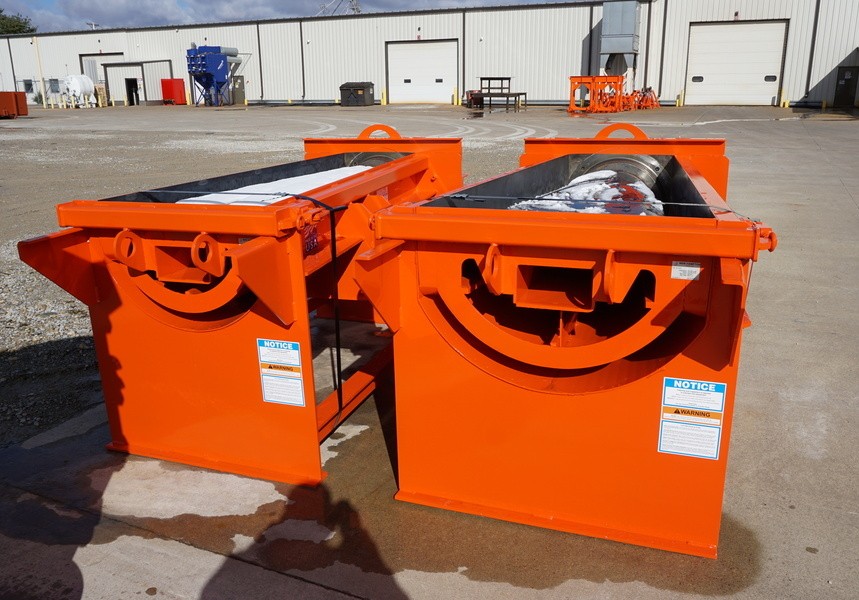
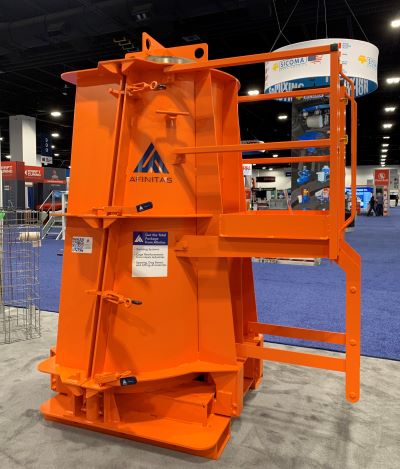
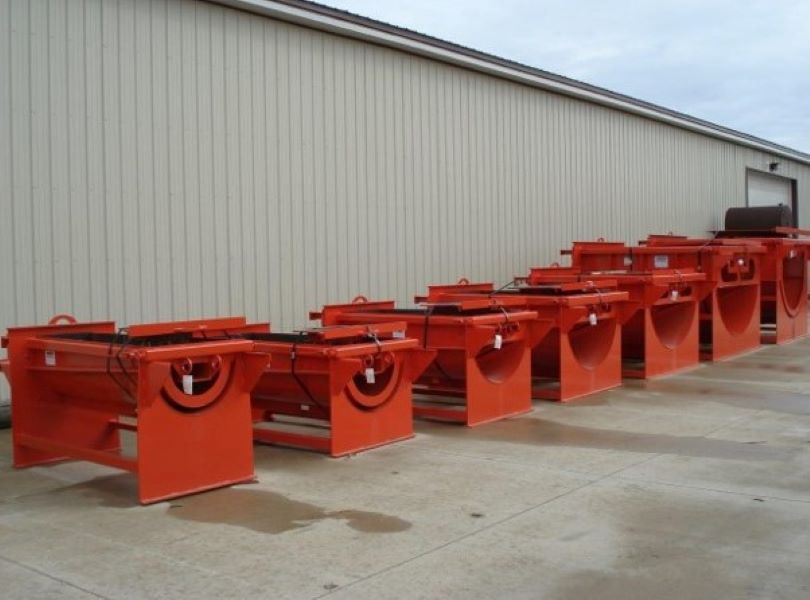
Heavy-duty flared end forming systems are designed in a wide range of sizes to meet your specific applications and state specifications. All equipment is fabricated from ¼” HR steel skin reinforced with 3/8” and ½” steel channel, ribs and gussets to reinforce material as needed to resist the given loads. All forms go through an iron phosphate wash prior to being coated with industrial primer and enamel topcoat paint.
Designed specifically for the traditional horizontal wetcast method of manufacturing flared end sections, this innovative system offers a perfect solution for creating high-quality flared ends with exceptional efficiency. Our precise design ensures consistent flared end structures resulting in an exact fit during pipe assembly.
The Afinitas Advantage
• Heavy steel construction, designed for strength, durability and performance
• Diameters 12″ through 96″
• Solid tapered form design with toggle clamps and alignment pins
• Solid tapered inner core
• Form includes two product retaining pins to retain the product when jack stripping the core
Flared End Form
Our NextGen forming systems have the same durability as our traditional forms but are more compact. In addition, they offer the ability to do vertical pouring which maximizes factory floor space.
The Afinitas Advantage
With NextGen flared end forming you’ll have:
@Afinitas