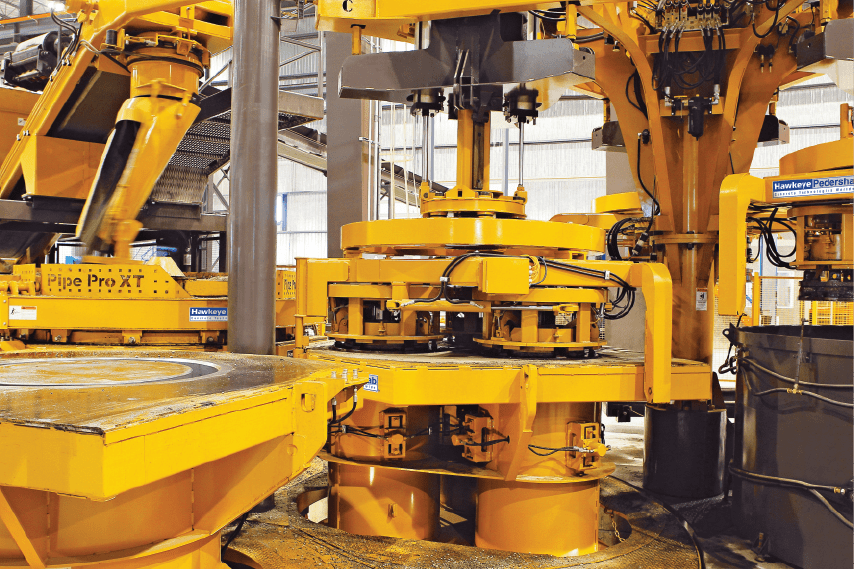
Flexibility, high output and automation to produce most of a typical concrete plant’s requirements is what you can rely on from Afinitas’ HawkeyePedershaab PipePro machine. Equipped with HawkeyePedershaab’s patented Multiform Modules, the PipePro machine manufactures up to four or eight concrete pipe (depending on the machine model) with each index of the machine. In our experience, PipePro’s combination of versatility and productivity is unmatched by any other concrete pipe machine. For example, producers can use the PipePro as a powerful stand-alone machine or integrate it into a fully labor-saving factory complete with automated post processing and handling equipment, testing, and curing systems.
Concrete Products
The PipePro machine is ideally suited to produce:
Capacity
Depending on the machine model, a typical PipePro plant offers an annual production capacity of 70,000-80,000 tons of product in a one-shift operation.
Models
- HawkeyePedershaab PipePro XT
- HawkeyePedershaab PipePro 96
HawkeyePedershaab PipePro | PipePro XT | PipePro 96 |
---|---|---|
Product Dimensions | 300mm to 1800mm diameter (12" to 72" diameter) | 300mm to 2400mm diameter (12" to 96" diameter) |
Product Lengths | up to 3.5M (12') | up to 3.5M (12') |
Maximum Multiforms by Machine | ||
Singleform | up to 72" diameter | up to 96" diameter |
Duoform | up to 30" diameter | up to 48" diameter |
Triform | up to 24" diameter | up to 39" diameter |
Quadform | up to 18" diameter | up to 30" diameter |
SixPak | up to 24" diameter | |
EightPak | up to 18" diameter |
PipePro Machine Key Advantages
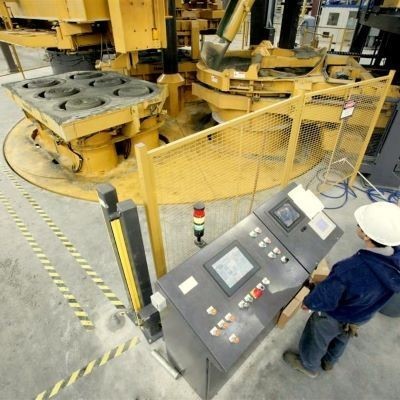
Fully Automatic Operation
With the PipePro, sophisticated programmable logic controller (PLC) hardware and software algorithms expertly manage your production cycle. Operation starts with a simple, menu–driven display screen that makes it easy to enter machine settings and product sizes. The PipePro machine takes it from there:
- A pan-type swipe feeder automatically positions over the form in the fill station and begins to feed and consolidate concrete by vibration into the form set.
- The PLC stores feed rates and vibration settings for each product type.
- PipePro’s carousel-style presshead picks and presses stay-in-place headers into the filled form set to form the spigot. The placement, pressing and troweling operations are completely automatic.
- Finished concrete pipe can be automatically offborne from the machine or manually removed with an overhead crane.
- Products are securely transported to the curing area within the form’s external jacket.
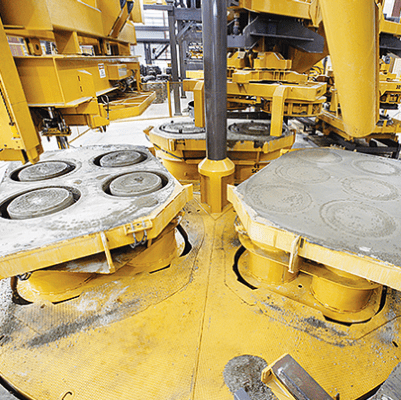
Three Station Productivity
The PipePro’s three-station turntable design collapses the filling, pressheading and stripping steps to fast-track the production cycle and increase output. Further, PipePro allows three different concrete pipe sizes or shapes to be manufactured simultaneously. This means with PipePro you are able to produce any combination of round, arch, and elliptical pipe as well as jacking pipe and manholes.
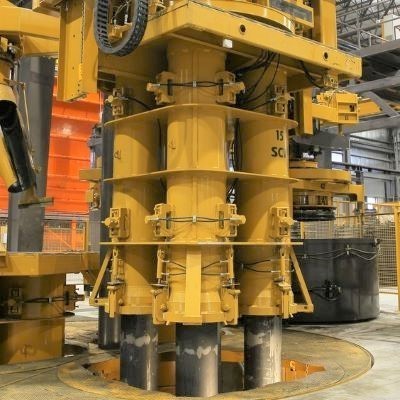
Multiforms Expand Output
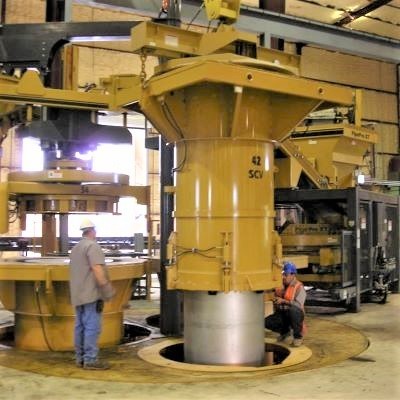
Quick Form Changeover
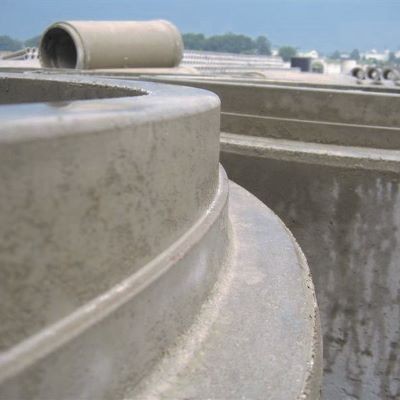
Consistent, Repeatable Results
PipePro’s computer-controlled feed rates and vibration settings are specific to each concrete product type to ensure quality. In addition, the PipePro’s pressheading system utilizes stay-in-place headers for smooth, dimensionally accurate spigots every time.