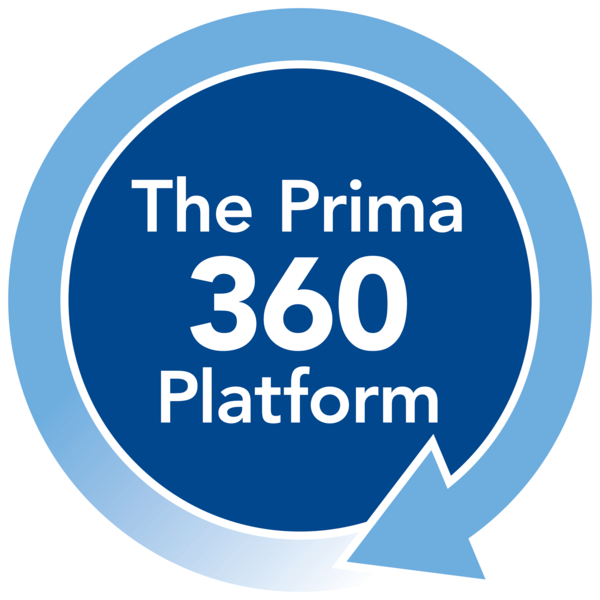
Production system for wetcast concrete slabs, veneers and other special concrete products
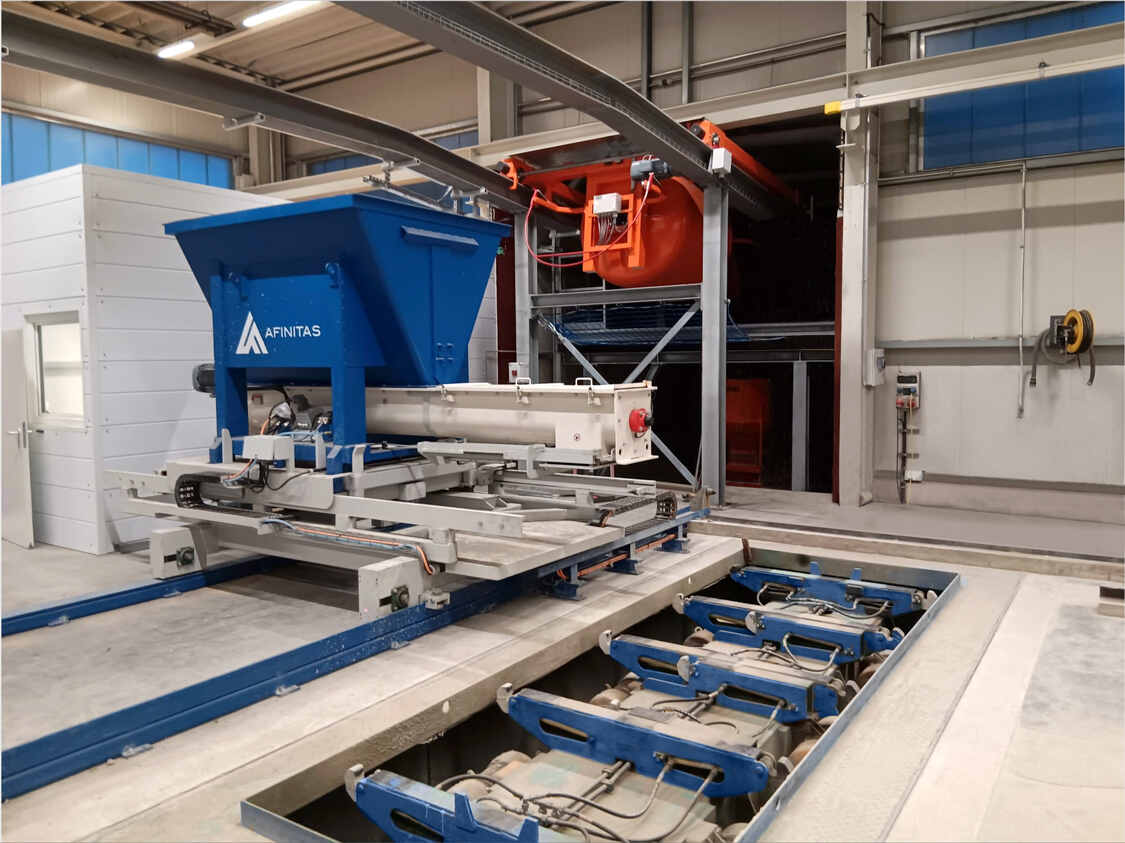
Prima Fit—as the name suggests—is wetcast automation that scales to fit your requirements. It’s a powerful, yet economical option that utilizes vertical product stacking to maximize floor space. In addition, Prima Fit can be easily configured to produce specialty precast structures that would require extra space and set up time on other systems. The flexibility and affordability of Prima Fit makes it an excellent choice to optimize your wetcast operations without breaking the bank.
Concrete Products
Prima Fit is ideally suited to produce:
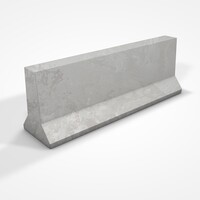
Median Barriers
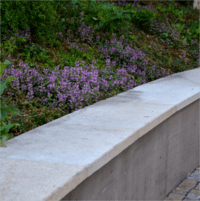
Retaining Walls
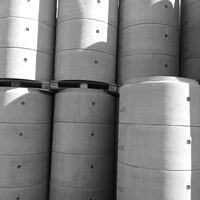
Manholes
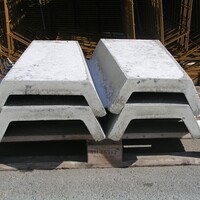
Road/Railway
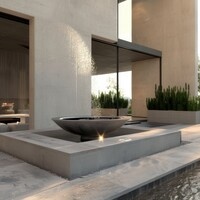
Specialty Products
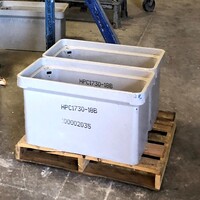
Polymer Products
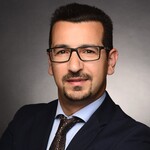
Interested in Prima Fit?
Email: Choukri Karabach (Product Line Leader) or call +49-175-220-1559
Chat with Choukri on WhatsApp
Prima Fit Product Features
The Prima Fit system for wetcast concrete product production is a modular system that uses a vertical stacking process to maximize factory floor space.
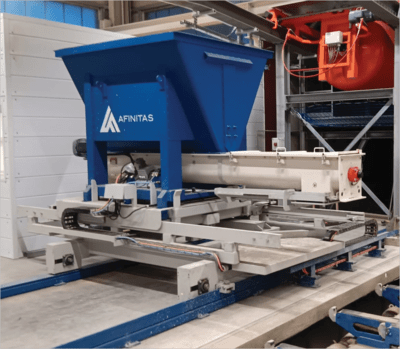
Concrete Filling
- Designed for dosing liquid concrete that can be conventional, lightly compacted or self compacted concrete (SCC).
- Concrete is conveyed via screw conveyor and filled in the mold via a metering slide valve and filling funnel.
- Available with a highly sensitive concrete weighing system to precisely dose concrete into the molds.
- Silo outlet is hydraulically adjustable in height so filling height can be adapted exactly to the mold.
- Mold contour can be traversed manually or via remote control or fully automated via a programmed path.
- Easy to clean as silo and dosing screw can be lifted out for cleaning and transporting to to washing station.
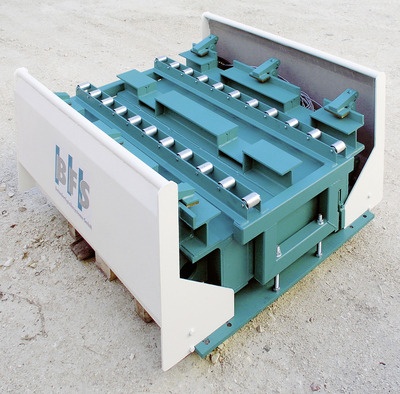
Filling Station and Vibration Table
- Specially designed system, switchable for compacting conventional concrete and shaking SCC.
- Depending on the direction of rotation, either a relatively small flywheel mass is set in motion at high speed for compaction or a large flywheel mass at low speed for shaking.
- The mold carrier pallet is moved to the vibrating table by a moving beam. The air springs lift the carrier pallet from the moving beam, and the pallet is hydraulically clamped onto the table.
- The vibrators are driven by electric motors via frequency converters.
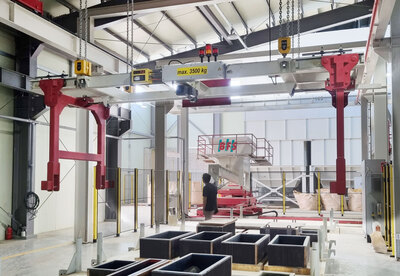
Crane Lifting
- Crane can be fitted with a double hock unit to operate different size molds.
- The transfer and stacking of mold carrier pallets can be done either manually with a crane lifting system, a rail-bound gantry drive
unit or via a fully automated high-bay storage system.
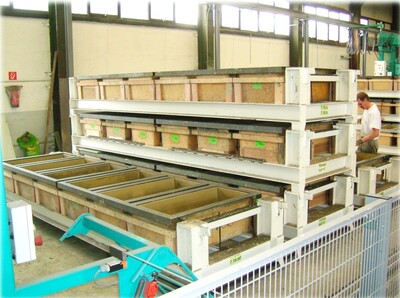
Mold Carrier Stacking Area
- Pallets are stacked vertically for storage and curing to optimize floor space.
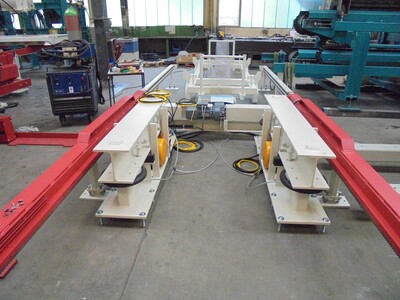
Demolding/Outfeed Line
- In the demolding station the hardened concrete products are taken out of the mold, turned and placed on a conveyor
belt. - Can be equipped with a vib-beam for demolding support.
- The production pallets are cleaned automatically and prepared for the next usage by the application of release agent in the spraying station.
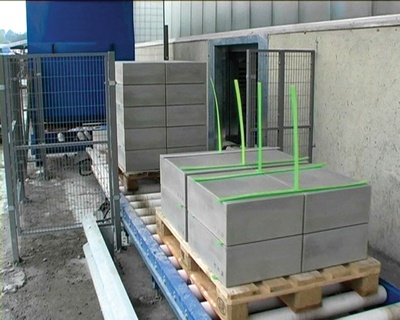
Product Transport
- Automated or via shuttle cart