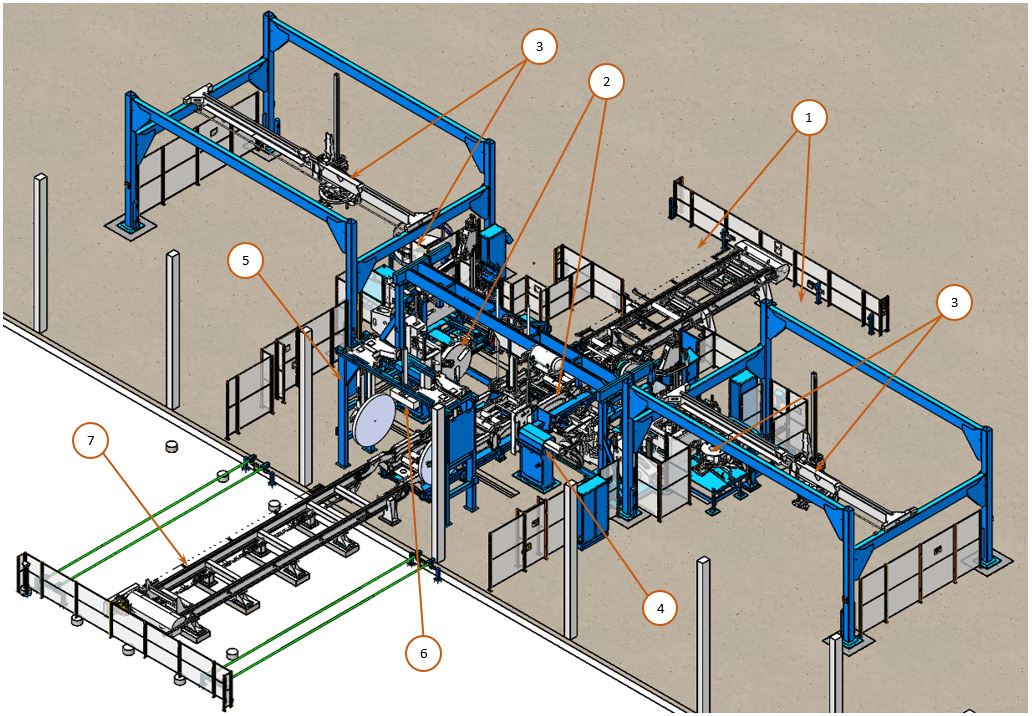
ROCO Handling equipment automates the removal of the pallet and header from the finished product, stacks the joint rings, and places the product on a conveyor for further processing or transport outdoors. Modules are available for automatic deburring, marking, vacuum testing, joint ring cleaning, storage and retrieval. ROCO handling equipment is designed for 12” (300mm) to 48” (1200mm) pipe and can be fully integrated into new pipe plants or added to existing pipe facilities as an independent system.
1. Transport
Cured pipe are transported to the ROCO infeed conveyor. Pipe can be automatically transported with a manipulator or horizontally carried (singly or in pairs) with a forklift truck. The infeed conveyor transports the pipes to the various post-processing stations.
2. Joint Ring Removal
An overhead clamp secures the pipe as twin manipulators clamp both the pallet and header. The joint rings are removed with a combination of pulling and pneumatic tapping. The removed joint rings are automatically fed to dedicated cleaners. The pipe advances to the debur station.
3. Pallet Cleaning, Storage, and Retrieval
The removed pallets are cleaned by a dedicated pallet cleaner. The cleaned pallets are picked and placed into a storage and retrieval area. Pallets are stored and await either automatic or manual retrieval. Pallets can also be stacked on handling skids for manual transport to the pipe machine or external storage.
3. Header Cleaning, Storage, and Retrieval
The removed headers are cleaned by a dedicated header cleaner. The cleaned headers are picked and placed into a storage and retrieval area. Headers are stored and await either automatic or manual retrieval. Headers can also be stacked on handling skids for manual transport to the pipe machine or external storage.
4. Deburring
The bell and spigot end of the pipe are automatically deburred. Rotating cones debur both the inner and outer edges of the pipe. Deburrers automatically adjust to the pipe diameter entering the system.
5. Vacuum Testing
Pipe are vacuum tested. Two closed cell neoprene coated platens press into the ends of the pipe and a vacuum is drawn. Vacuum is held for a preset time and pressure. If the pipe passes the vacuum test, the platens automatically release. Otherwise an alarm sounds. Results are measured and recorded.
6. Marking
The barrel of the pipe is marked with an inkjet printer. Both internal and external markers are available. Markings can include pipe size and class, date of manufacture, vacuum test, and manufacturer’s name and logo.
7. Pipe Exit
An outfeed conveyor transports the completed pipe outdoors for yarding. System is designed so that multiple pipe can be picked from the outfeed conveyor and transported to the storage yard.