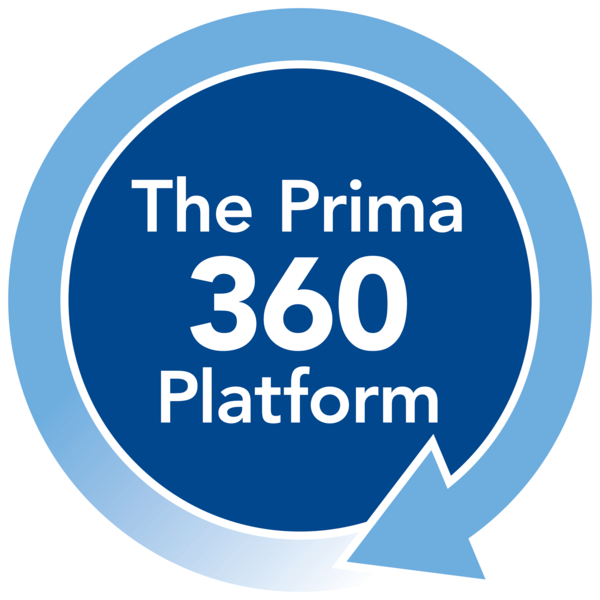
Assembly line efficiency with automated work stations for the production of nearly any type of infrastructural precast product.
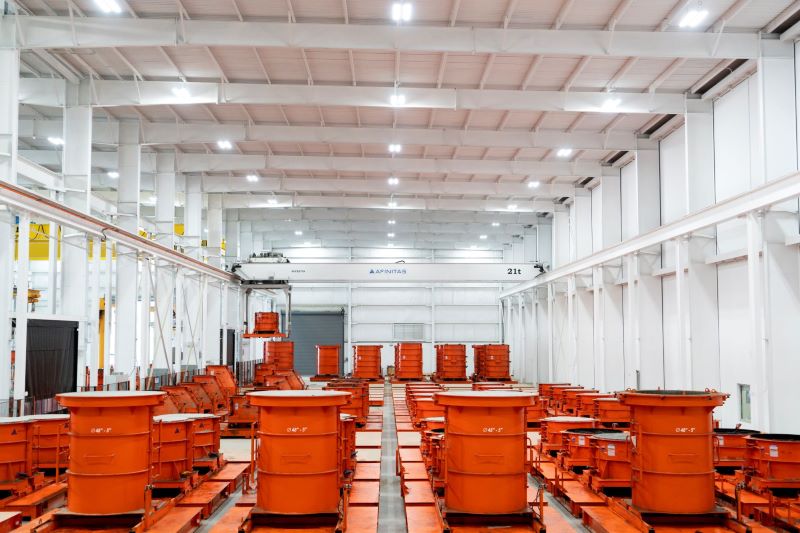
Traditional wetcast production plant setups make it nearly impossible to drive productivity. This is because so many variables are at play. Most wetcast production plants lack a process flow that can be easily tracked, measured, analyzed and optimized.
Afinitas helps you eliminate these challenges with our Prima Wetcast Automation System.
Prima is a fully automated system that allows precasters to organize their work stations to track and measure productivity in real time.
The efficiency and labor savings offered by a Prima system is a game changer for precasters who produce standard and made-to-order concrete products.
Concrete Products
What can be produced with the Prima Wetcast System?
The Prima wetcast automation system manufactures a wide range of concrete products, including pipes, blocks, manhole risers and bases, rings, spetic tanks and more. Prima can also be used to manufacture any custom precast concrete products, including landscaping products, concrete blocks, and retaining walls. This system is ideal for any application that develops products in wetcast form.
”After reviewing several systems, we decided on Prima because of the relationships we've had with several of the Afinitas companies."
Joel SheetsVice President and General Manager, Tindall Corporation, Utilities Division
Prima Wetcast Automation Key Advantages
Full automation of your precast concrete production processes has several key advantages. The Prima wetcast automation system is designed to make your wetcast production line safer, more productive, more accountable and more organized. Here’s how a fully automated wetcast production system can help your business:
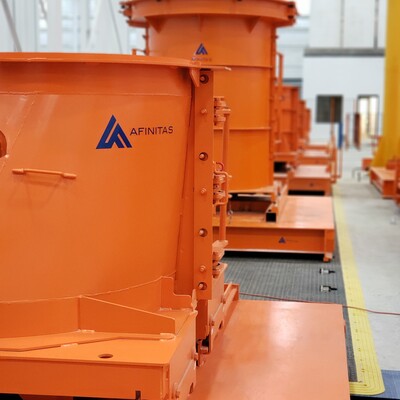
Reduce Labor and Increase Productivity
In contrast to many wetcast operations where the forms are stationary on the floor, Prima introduces a system where the forms automatically circulate in a loop through specialized workstations. These workstantons break the process down into steps such as demolding, mold cleaning and oiling, reinforcement, form filling and ultimately curing. Created in accordance with lean manufacturing and 5S workplace practices, these specialized workstations enable faster turnaround by eliminating unnecessary tasks. Consequently, the labor needed is significantly reduced. Here’s how the Prima workstations flow:
- When all operations at a given workstation are completed, the station is reported “ready” in the Prima system and the operators can move to other workstations.
- When all workstations have reported “ready” the molds all move one position forward on the assembly line for the next operation.
- This linear process offers a significant increase in productivity compared with other wetcast systems on the market.
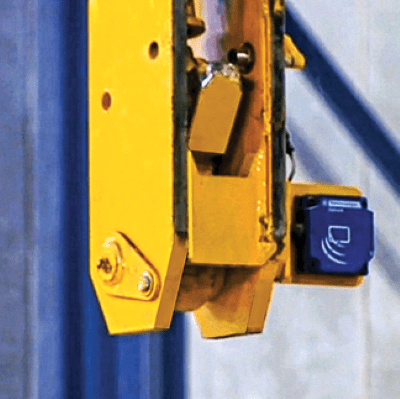
Track Production Metrics
An RFID tagging system uniquely identifies the form and tracks its status to provide information on process time, reinforcement and filling requirements.
The Prima wetcast automation system allows operators to prepare and efficiently execute the necessary operations for each form. As each work station is required to acknowledge when its operations are complete, the Prima system tracks the time consumed for each form.
This feedback exposes bottlenecks and gives the manager information to further improve the production processes. In fact, team members can manage the process down to the piece. Prima also offers a real-time production tracking screen in the plant so the operators know immediately if a workstation falls behind the schedule and can act accordingly to get it back up to speed.
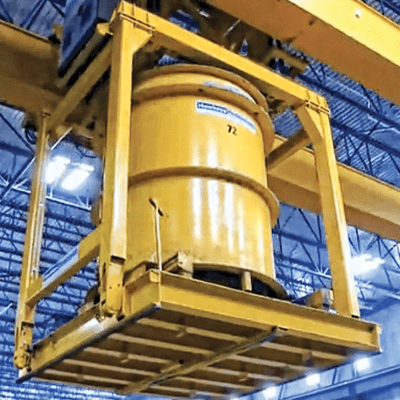
Improve Plant Safety
The Prima wetcast automation system is fully safety compliant, and it significantly improves safety compared to many traditional wetcast production facilities. Prima eliminates the need for forklift trucks in the production area and there is no overhead transport of products or concrete buckets. Furthermore, the specialized workstations can be ergonomically designed (e.g. with tool balancers so the operators do not have to work with heavy loads in inconvenient positions).
The result is a safer, more productive work environment.
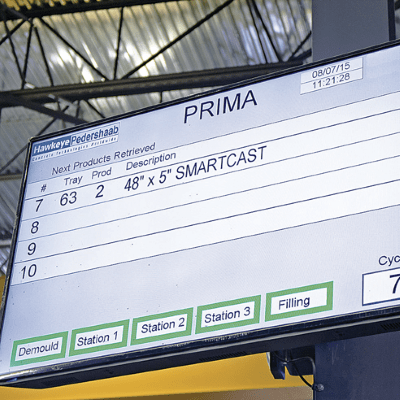
Simplify Production Planning
When planning a given day’s production all the historical data for the relevant wetcast forms can be accessed with the Prima system. The production manager can analyze the demand for concrete and manpower throughout the day and appropriately coordinate the queue to optimize throughput and labor. This information can be used to build a production plan that is realistic and feasible and identifies potential bottlenecks before they become a problem.