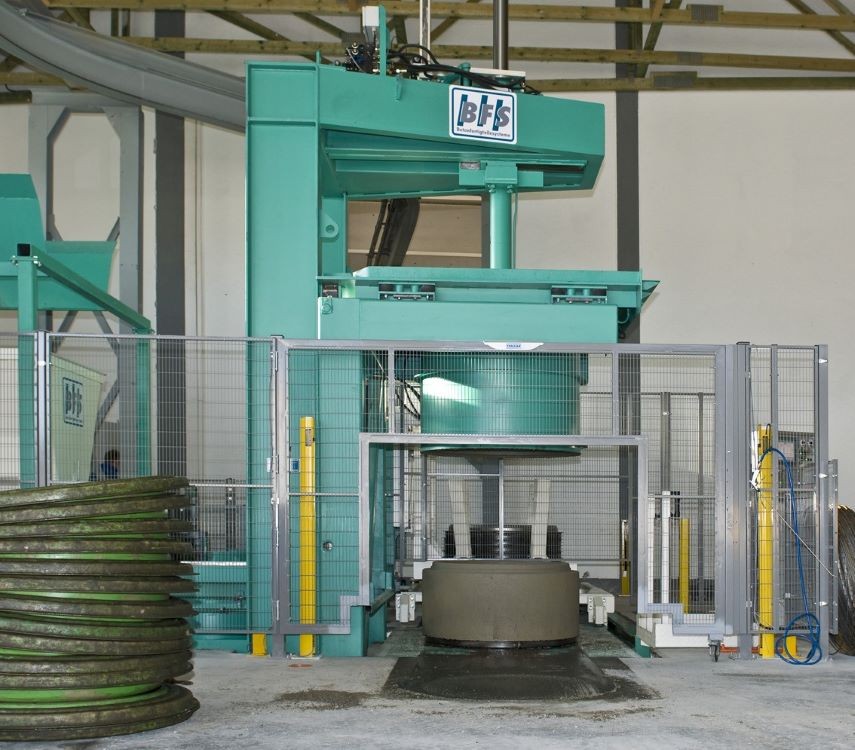
With the BFS Karibic, Afinitas enables producers to manufacture many varieties of concrete products with high quality and virtually unlimited customization. The Karibic machine can be used as a simple, standalone unit or can be equipped for complete automation of the production process. Many producers choose the BFS Karibic for its short changeover times that guarantee optimum machine utilization.
Concrete Products
The Karibic machine is ideally suited to produce:
Capacity
Depending on the machine model, a typical BFS Karibic plant offers an annual production capacity of 70,000 tons of product/year.
Models
- BFS Karibic 800
- BFS Karibic 1200
- BFS Karibic 1500
- BFS Karibic 2000
BFS Karibic | BFS Karibic 800 | BFS Karibic 1200 | BFS Karibic 1500 | BFS Karibic 2000 |
---|---|---|---|---|
Product Dimensions | 100mm to 800mm diameter (4" to 32" diameter) | 100mm to 1200mm diameter (4" to 48" diameter) | 100mm to 1500mm diameter (4" to 60" diameter) | 100mm to 2000mm diameter (4" to 78" diameter) |
Product Lengths | up to 1300m (60') | up to 1300m (60') | up to 1300m (60') | up to 1300m (60') |
BFS Karibic Machine Key Advantages
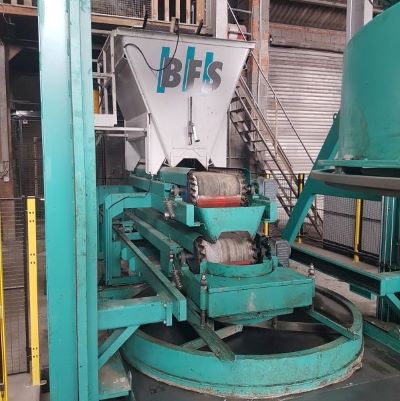
BFS Karibic is Simple to Operate
With the BFS Karibic, the system does the work. Whether using single (Karibic Mono) or double (Karibic Duo) production, the Karibic does not require highly skilled labor and can be operated by one person. Here’s how Karibic works:
- From the base pallet magazine, the Karibic pusher system moves one pallet to the release agent spraying station and then into the concrete casting position.
- The generously dimensioned hydraulic aggregate with state-of-the-art proportional valve technology ensures output reserves, operational reliability, and fast cycle times. The clear structure of the modules enables simple, quick maintenance.
- Concrete compaction is performed by a central vibrator with hydraulic mold core clamping. The frequency-controlled direct drive is powered by dynamic electric motors with a large RPM range. BFS technology ensures a maximum application of vibration forces to the mold equipment with minimum noise.
- After demolding, the products can be automatically transported out of the production machine for curing with a computer-operated BFS ROBOTRAC system or by the agile BFS electric trolley.
- During curing, the spigot-end ring remains on the concrete products, resulting in high dimensional accuracy and roundness of the spigot-end profile.
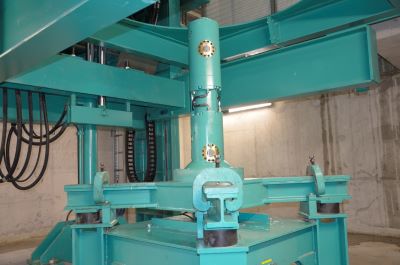
Powerful Central Vibrator
Concrete compaction is achieved via a modern central vibrator with hydraulic mold core clamping. The frequency-controlled direct drive is powered by dynamic electric motors with a large RPM range. The BFS-typical vibration cross with sophisticated vibration insulation against the foundation, ensures maximum application of vibration forces to the mold equipment with a minimum of noise.
- An automatic grease lubrication system is an option that can be added.
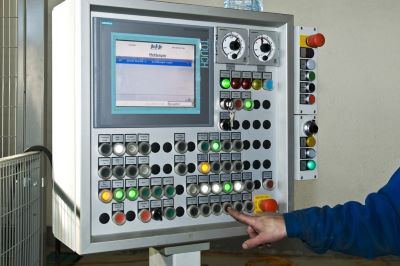
One-Person Can Operate the BFS Karibic
Karibic’s high tech control panel makes it simple for one worker to control the production flow, including mounting parts, intermediate storage and concrete product removal.
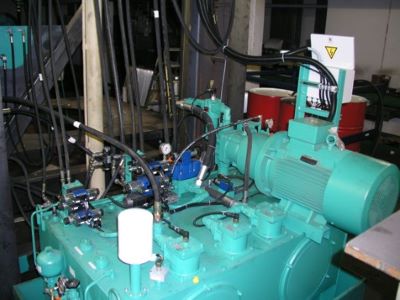
BFS Karibic Hydraulic Powerpack
The generously dimensioned hydraulic aggregate with state-of-the-art proportional valve technology ensures output reserves, operational reliability, and fast cycle times. BFS Karibic’s clear structure of the modules enables simple, quick maintenance.
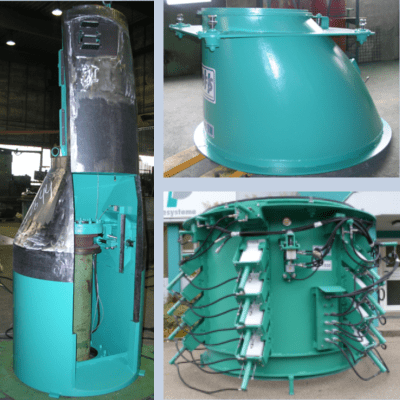
Mold Variety
BFS Karibic’s modular mold system allows different components to be combined in a wide range of mold dimensions. Mold cores, jackets, base pallets and spigot end shapers are all part of BFS’s homogeneous system that reduces your investment costs and increases concrete product production flexibility.
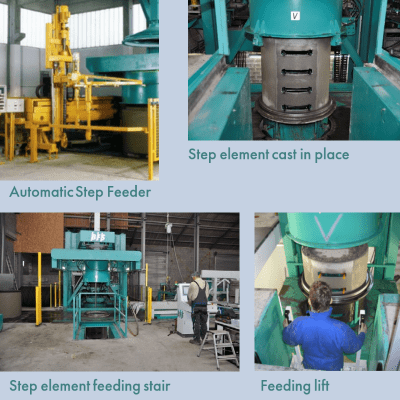
Step Element Cast in Place System
With Karibic, step elements can be inserted manually, semi-automatically or automatically into the mold unit. This can also be done in conjunction with, and at the same time as, inserting the steel reinforcement hoops. BFS has a patent on this process. Reinforcement and step elements, such as cast iron or rungs, are then automatically cast-in-place during compaction.
Afinitas adds more automation to your production flow: