Equipment & Automation
Here for the life of your equipment.
At Afinitas, we don’t just sell equipment — we stand behind it for life. From labor-saving automation, to advanced formwork and accessories, our products are backed by global technical support, deep industry experience and a robust parts inventory. We are your trusted partner for delivering performance, service and reliability every step of the way.
Learn about how our Afinitas Alliance Service and Parts Partnership Programs can help you achieve peak performance and minimize downtime. We tailor these programs to your equipment and needs. Our comprehensive offering includes partnership programs for:
- Machine Preventative Maintenance
- Form Maintenance
- Curing Systems Maintenance
- Plant Optimization
- Tech Support and Training
- Spare Parts Plans
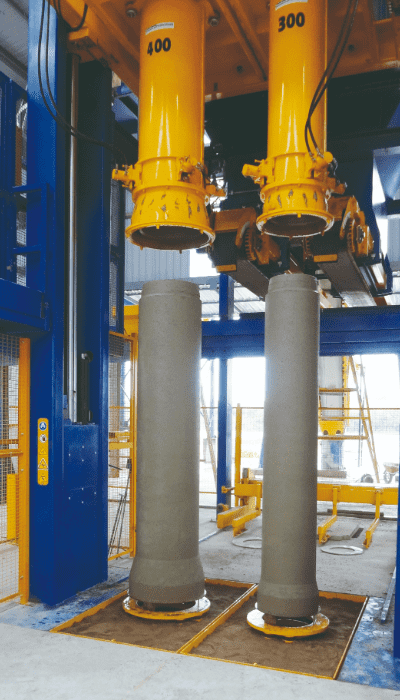
For quick service and general assistance, please complete the form below and a representative will be in touch with you shortly.
Learn About Afinitas Alliance Services
Alliance Service Overview
Our Alliance Service Programs are most optimized for multi-year partnership agreements where our field professionals help to identify risks that may create downtime and product deficiencies. These assessments occur during regular service visits scheduled to fit your particular needs. During your planned visits, our field professional will evaluate your equipment, identify problem areas, and provide professional guidance for repairs and maintenance, as well as system updates and enhancements.
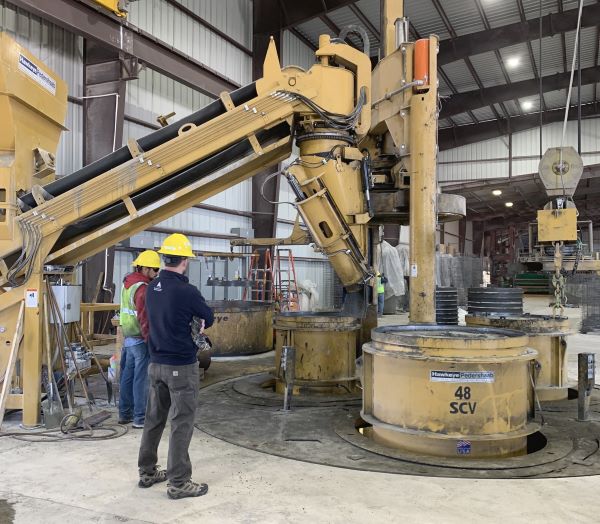
Machine Preventative Maintenance
Our Machine Service Partnership Programs offer increased focus to our preventative maintenance and plans for repairs and improvements. As part of our inspection, we’ll communicate the critical wear points and maintenance needed to your team. In addition, we’ll evaluate wear and spare parts inventory, to avoid downtime and suggest machine upgrades/replacements to increase efficiency and reliability. The Afinitas technician will issue a written
inspection report detailing all of this information along with recommended actions. Equipment Evaluation List:
• Hydraulic and Pneumatic Power Source
• Electrical System and Controls
• Power Transmission (wheels, belts, gears, bearings)
• Operator Console or Interface
• Actuators (cylinders, motors)
• Specialized Parts on Equipment
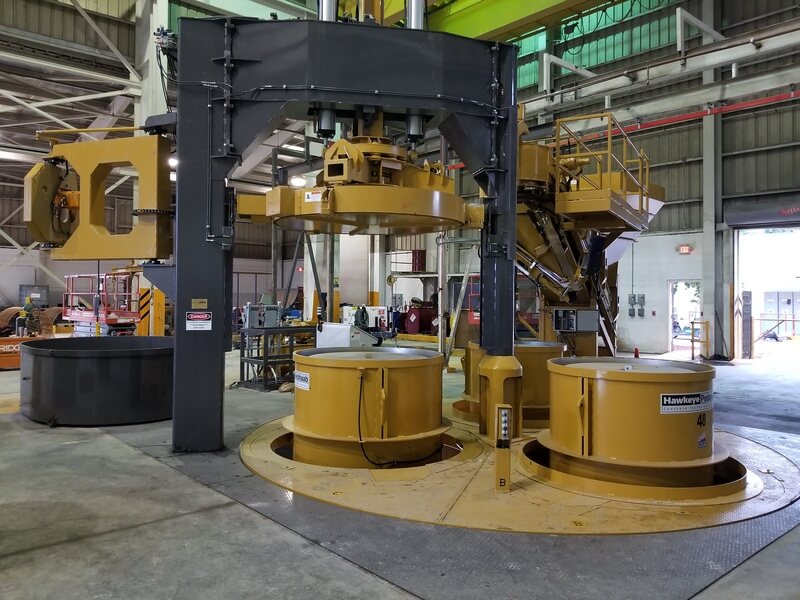
Form Maintenance
General List of Equipment Evaluation:
• Hydraulic and Pneumatic Power Source
• Electrical System and Controls
• Power Transmission (wheels, belts, gears, bearings)
• Operator Console or Interface
• Actuators (cylinders, motors)
• Specialized Parts on Equipment
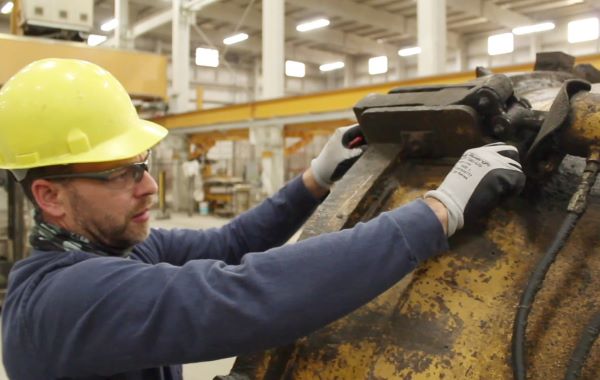
Curing Systems Maintenance
Our goal is to ensure you have the curing solutions that are best suited to your needs to produce durable, quality products with high efficiency and minimal downtime.
- Technical Support and Training
- Installation and Turnkey/Retrofit
- Start Up Service
- Replacement Services
- System Maintenance
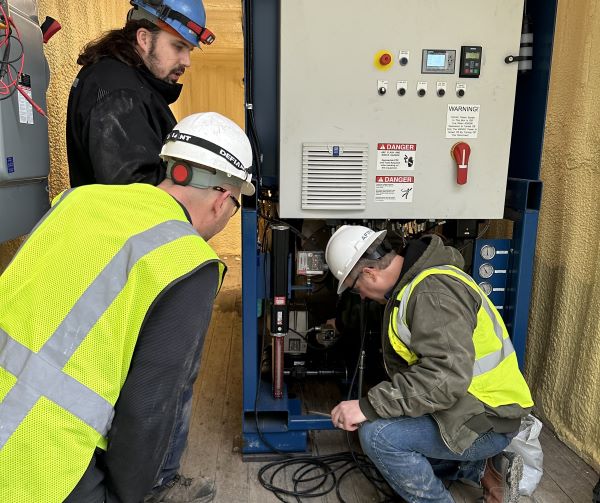
Plant Optimization
Afinitas has experienced technicians available to evaluate the operation and maintenance of your machinery. Our technicians are involved with pipe production in plants throughout the world and our plant evaluation process can result in large operating benefits for your plant. During the site visit we evaluate both your mechanical equipment and audit your production practices. Both areas are critical to the consistent and efficient production of quality products. We identify problem areas and provide suggestions for equipment enhancements, recommended parts inventory, and a wide range of other
solutions. Additionally, we can personally assist your team to implement the suggested changes into your operation. Simple repairs are included in the visit.
Objectives of the Plant Optimization Process:
• Bring a focus on safety, quality, quantity, in that order of priority.
• Communicate the critical safety areas for all personnel.
• Evaluate your product quality and provide guidance for consistent assessments beyond typical specifications.
• Observe your operation and team in action using our audit tools to identify key areas of improvement.
• Provide a written report of the visit with recommended actions.
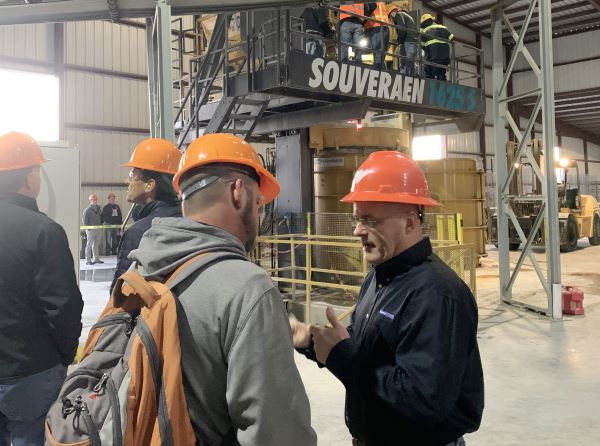
Spare Parts Plans
In the fast-paced precast concrete production environment, unexpected equipment failures can bring operations to a grinding halt — causing costly downtime, missed deliveries and unnecessary stress. With Afinitas Spare Parts Plans, you can take control of your operation’s reliability by ensuring you have the right parts when you need them most. We offer three different tiers of service and can tailor plans to meet your needs:
Essential Spare Parts Plan – Basic consumables like filters, belts, cleaner components among other common wear parts.
Advantage Spare Parts Plan – Includes all the basics, plus additional valves, sensors, electrical and sub-assembly components.
Premium Spare Parts Plan – Ideal for those with similar equipment across multiple sites. Comprehensive coverage, eliminates wait time on key parts.
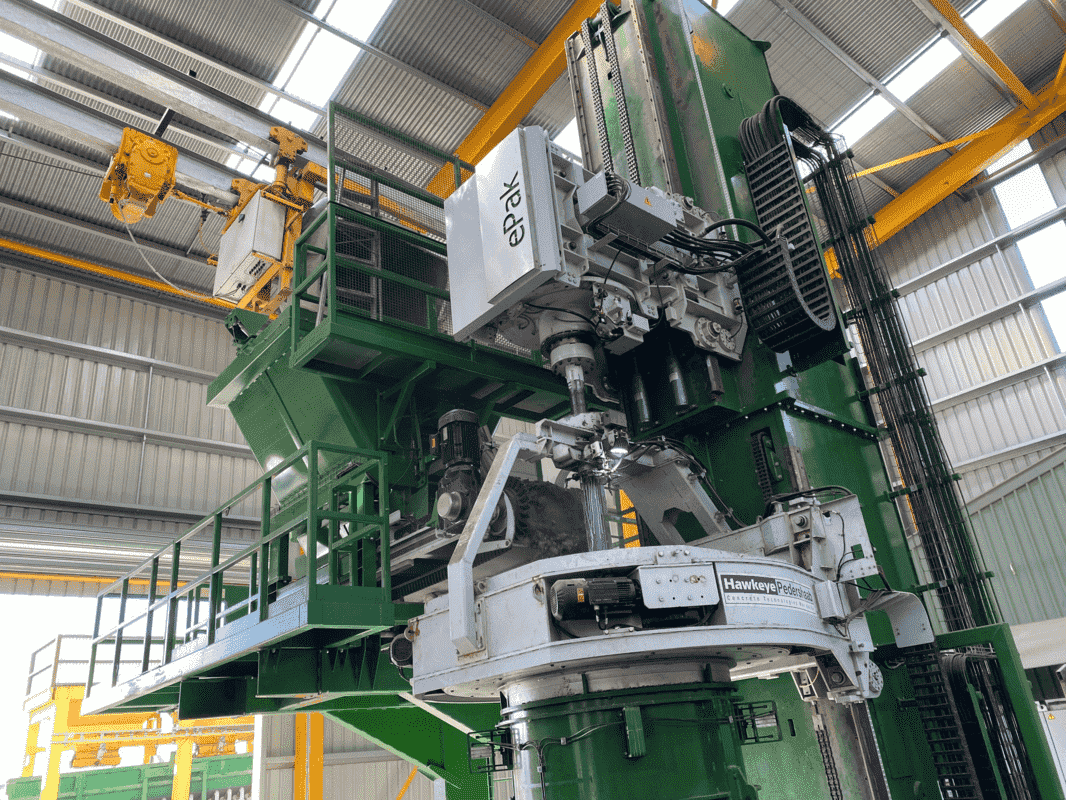
Contact Parts Team
General Inquiries
USA (HawkeyePedershaab) +1-319 394-2240 email: hawkeyeparts@afinitas.com
Denmark (HawkeyePedershaab) +45 96454172 email: aftersales@afinitas.com
Germany (BFS) +49 7344 9603-77 email: BFS.spareparts@afinitas.com
Contact Services Team
General Inquiries
USA (HawkeyePedershaab) +1-(319) 394-2270 email: hawkeyetech@afinitas.com
Denmark (HawkeyePedershaab) +45 96454050 email: service.dk@afinitas.com
Germany (BFS) +49 7344 9603-55 email: BFS.service@afinitas.com